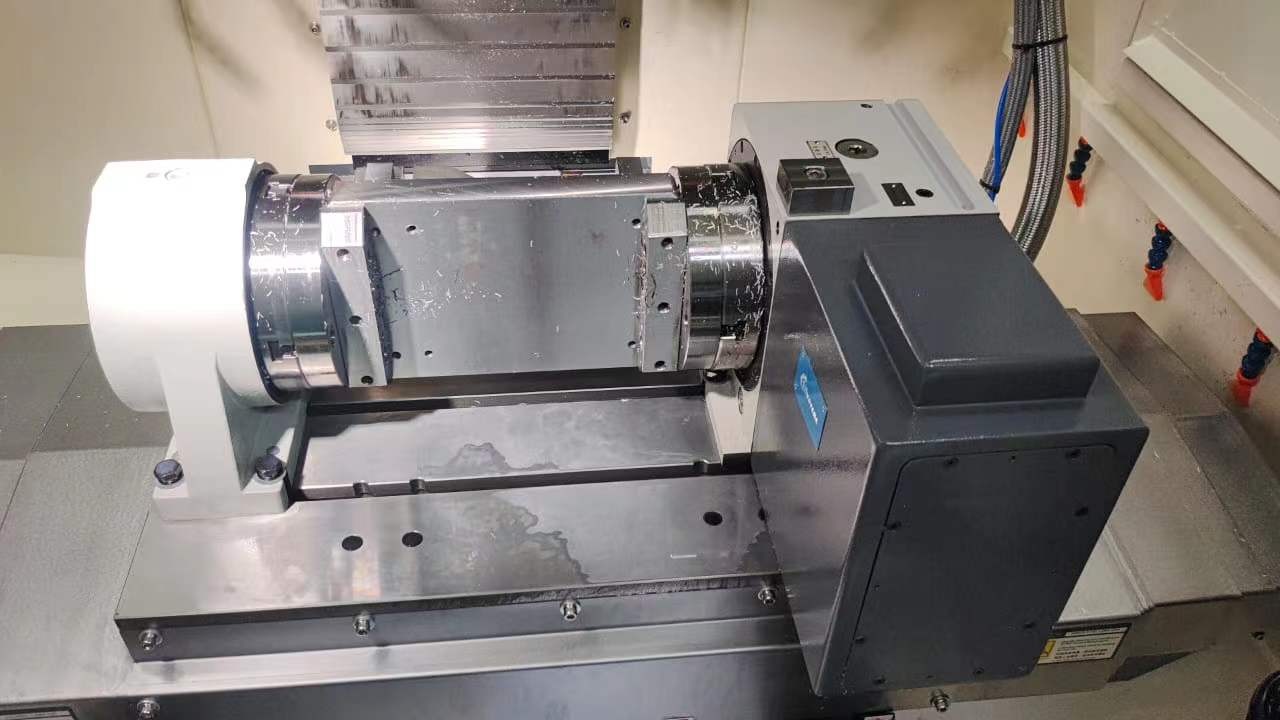
The fundamental concept behind a rotary table is to hold a workpiece in place while rotating it along a precise axis, allowing for accurate part machining. The workpiece can be more precisely worked with metal thanks to the rotary. For manual applications, a table might be employed. On a CNC machine, however, it can also be installed and used. Numerous operational advantages that increase the capabilities of your CNC machine come with adding a rotary table.
Adaptable
Increased machine versatility is one of the critical advantages of adding a table to a CNC machine. You can extend the functionality of your machine without spending money on a new one by adding a turntable. The cost of expanding the functionality of an existing machine is much lower than buying a brand-new one, increasing its usefulness. The device is made more versatile and practical by adding a turntable.
Greater accuracy
Your current CNC machine can handle more intricate tasks more accurately if you add a rotary table. Precision metalworking is made possible by the table, which fixes the object being machined in position. Thanks to this, you can now produce more complex masterpieces that require more meticulous work.
Increased production
Not the cycle time, but the working time corresponding to the longest operation determines output. In actuality, during processing, parts pass through various stations. Due to the simultaneous processing of multiple parts, the finished product’s cadence does not match the cycle time. As a result, the most thorough editing comes after the work is finished, and time needs to be clarified by several edits going on at once.
Saves time
A fantastic approach to speed up production is by adding a rotary table to your CNC machine. With a rotating table, you can use the same machine to do more complex jobs. These finishing tasks can be completed on the same device rather than moving the object to another to finish the investigation. The total production time for an item is reduced when all fabrication and finishing processes are carried out simultaneously on the same equipment.
Increased welding quality
By allowing the welder to weld at the appropriate place after rotating the positioner to that position, rotary welding tables enhance the quality of the weld. Welders can adjust the height and angle of the surface using these tables. This makes the job simpler to repeat and increases the welder’s visibility. Each benefit raises the quality of the work product.
Enhanced safety
Especially when situating large workpieces, rotating welding tables increase workshop workers’ safety. Another benefit of a rotating welding table is that it lowers the possibility of workplace hazards because the welder doesn’t need to utilise ladders or other climbing apparatus to raise the workpiece’s height. Cranes and forklifts were once employed to rotate workpieces, but this was ineffective and put workers at risk. A rotary welding table provides a rotating surface, lowering the danger. The process of mounting workpieces on the previous machines required extensive employee training. However, with the help of these turntables, any worker may manage assembly in a matter of hours.
Improved CMM capability
A CMM is most frequently used with a stylus to collect measurement data. This implies that the component to be measured must be reachable from all directions. This can become an issue when working with more essential parts close to the CMM’s table size. In these circumstances, the portion can be turned to face the stylus on a turntable. This lessens the amount of gantry movement necessary and permits you to move to a position from which you can reach the area’s edge if it is inaccessible from a static position.